CIVA is a powerful and easy to use tool, but discovering all of its numerous possibilities may take you some time. That is why we offer you here all the CIVA Tips we published in our Newsletters, to help you master it faster!
Internal and external counterbore slopes around a parametric weld in CIVA UT (May 2025)
For the specimen profile to be valid, it is necessary to respect the construction constraint of a welded metal thickness smaller than the base metal thickness. The addition of counterbore slopes (symmetrical or not on either side of the weld) is compatible in planar and cylindrical weld configurations, thus allowing the construction of plate, tube, tube and elbow junction. This new CIVA functionality then allows the evaluation of the sensitivity of a UT inspection process to variations in slopes around a weld in the context of parametric studies!
Noise addition in post-processing (November 2024)
To use this tool, simply select the "Noise Addition" post-processing option once you have run your simulation, as shown in the screenshot below.
Once you have selected this tool, all you have to do is set the noise level in "points". For example, if the maximum of your simulation is 16 points and you set the noise level to 1 point, you will obtain a signal-to-noise ratio of approximately -24dB. The image below illustrates the result of this post-processing.
Temperature gradient in the wedge (September 2024)
This variation of temperature is defined from a temperature gradient law. The option is available in the probe panel, under the wedge tab, then in [material] / [properties] / [homogeneity type], as illustrated in the figure below.
CIVA then uses the continuously variable model for the wave velocity in the wedge. This will have an impact on the beam distortion / deviation.
Link parameters during parametric studies (July 2024)
For multiparametric studies, it may be necessary to link some parameters together. Indeed, some parameters can be correlated by nature, which means they cannot vary independently from others (for example, length and height of a crack are usually linked). You may also wish to focus on some specific combinations or reduce the number of independent parameters to limit the amount of simulations to perform, or iterate on specific influential parameters obtained from the combination of different inputs (for example, the surface of a flaw). To do that, CIVA provides the possibility to define formulae allowing to link one parameter to another, variable one.
Let's take the example of a weld inspection scenario, where you wish to study the results obtained for different defects located in the Heat Affected Zone (HAZ).
Due to the weld chamfer profile, moving the flaw in the HAZ will require linking the flaw depth and the flaw's axial position. This is possible in CIVA with a formula.
First, you define both parameters as variables, by selecting them with the relevant contextual menu in the flaw panel.
In the Variation panel, the flaw ligament (called "FLAW_LIG" here) is monitored with a linear spacing of 10 values between 0 and 5 mm. It corresponds to a "characteristic" type of variable in CIVA. By selecting the type "Formula" for the flaw's Y position parameter (named "FLAW_POS" here, which corresponds to the distance to the weld's center), you can then key in a mathematical relationship between this parameter and the previous one. Note that two other parameters were involved in this example of parametric study: the probe's refraction angle and the probe's standoff (distance to the weld center).
To do so, each parameter can be used in a formula with their TAG name (customizable by the user) and mathematical operators are available to build your formula (see tables hereafter). In this application case, a simple linear function "-21+FLAW_LIG" has been entered to monitor the flaw's position along the HAZ depending on its depth, but you have of course many other possibilities!
To make sure that you have defined relevant formulae, you can use the preview buttons in the Variation tab to check in the 3D view that the defined variations are consistent with your design of experiments.
Flexible wedge (May 2024)
In CIVA, the flexible wedge option can be found under "Probe" > "Wedge" > "Geometry" > "Rigidity".
Once the flexible option is selected, the color of the probe will turn blue in the 3D view, and the wedge will adapt to the surface so that the emergence point is in contact with the part, as illustrated below.
Note: The probe modeling parameters (in the "Probe" panel) are the same for both flexible and rigid wedges. However, the positioning options for a flexible wedge probe are the same as those for immersion inspection, offering more possibilities.
Import of 3D CAD files into CIVA RT/CT: Volume loading order (March 2024)
To ensure that CAD parts are correctly interpreted in CIVA and that the result is realistic, the internal volume must be loaded first.
To ensure that materials are correctly assigned, use the "Material" option available in the toolbox. By tracing a ray between the source and a detector pixel, you'll be able to visualize the different materials passed through and their thicknesses, and thus ensure that the order of the different CAD files is correctly interpreted by CIVA.
Complex components in CIVA SHM (January 2024)
However, the "Specimen" panel in the CIVA GUI still only includes two geometries: Planar or Cylinder.
Indeed, these complex components are built from initial profiles of planar and tubular specimens.
The SHM module relies on a spectral 3D FEM method where the mesh is fully driven by the software. This mesh is first initiated from a simple geometric profile, before following the geometrical transformations applied to it in order to create the final complex geometry of the component with its adapted and structured mesh.
Therefore:
- From a planar component, it is in the "Curvature" panel that you can create specimens with irregular shapes, via the definition of a unique median profile, or through 2 different profiles applied on the upper and lower part of the plate, leading to a variable thickness.
- From a tubular component, it is also in the "Curvature" panel that you can create an elbow, generated from the initial cylinder.
- From a multilayers tubular or planar component, it is through the "Stiffener" panel that you can create a "Sleeve" on the specimen, by defining on which layer and along which length this sleeve is positioned.
Define tilted flaws in Civa ET (November 2023)
Since CIVA 2023, it is possible to define complex shape components in the Inspection Simulation (3D) module. These complex shape components can be obtained either from predefined geometries (blade root or groove, weld profiles) or from a 2D CAD profile extrusion. Some examples of complex geometries can be seen below.
Contrary to canonical geometries, for which the simulations are managed by a semi-analytical method with reduced computation times, but for which there are some limitations, complex components are solved with a numerical method ("FIT" method, for "Finite Integration Technique") through which there are less limitations on the shape of the component, but also on the flaw orientation, which is no longer necessarily perpendicular to the component surface.
Although with this type of component, in CIVA 2023, the plate and flaw geometry is considered as invariant in the extrusion direction, it is now possible to study the impact of the flaw tilt on the measured signal. Results below show the signal obtained for two flaw tilt values: 10° and 40°. And if you want to modify the flaw tilt in a simple plate, you just have to define the specimen geometry as a 2D CAD one and you will be able to control this angle.
The superimposed curves are visible on the following picture, that shows the impact of the flaw tilt on the amplitude, the phase and the shape of the measured signal.
UT pre-processing in parametric study (September 2023)
- Force compute the delay law
- Force compute TCG (calibration)
For each variation included in the parametric study, a pre-processing allows you to automate the calculation of a setting that must be carried out manually in the CIVA model. Typically, this can be the calculation of the delay laws for a phased-array transducer or even a TCG calibration from the "Simulated TCG" tool.
By default, no pre-processing is enabled. This means, for example, that the laws calculated in the model will be applied as they are to each variation/calculation of the parametric study. It is necessary to activate pre-processing in order to update the settings (for example the delay laws) for each new variation. The same process is considered for automatic TCG calibrations.
Whether to activate pre-processing or not depends on the objective of the study.
Example
We consider a phased-array transducer whose laws have been calculated from a reference material. The properties of this material are defined as variable parameters.
Two scenarios are then possible:
- The first consists in evaluating the impact of the change of material by considering the initial phased-array setting. In this case, it is not necessary to activate the recalculation of the delay laws.
- On the other hand, if the objective is to readjust the laws for each new material considered in the parametric study, the option must be checked (e.g., to maintain a constant deviation angle).
Thus, when defining the CIVA model, it is important to check if variable parameters can have an impact on the settings, and whether it seems necessary to force the recalculation of these settings according to the objective of the study.
SuperBatch (July 2023)
- No need to run calculations manually, one by one
- Reduce calculation times by making better use of multi-core machines and parallelizing calculations
- Simulations can be added to an already running batch at any time
- In the event of unexpected interruption of a calculation in parallelization mode, all tasks performed are automatically saved and do not need to be recalculated
There are two ways to use the Batch Manager and perform the calculations:
- "Traditional" mode: no parallelization, CIVA files are calculated one by one according to the defined list of simulations
- "Parallelized" mode: CIVA files and task groups are calculated in parallel
Traditional mode
There are three stages in defining a batch calculation in traditional mode (see the image below):
- Load the predefined simulations to be processed
- Keep default calculation parameters: "Number of executors" = 1, "Splitting" option disabled
- Select the desired simulations from the list and run the batch calculation
Note: Even when running a batch in traditional mode, several cores of the machine can be used. Each CIVA simulation is based on a specific algorithm with a given level of parallelization depending on the technique and type of calculation. Thus, when the algorithm used is already efficiently parallelized, calculation times between traditional and parallelized batches will be close.
Parallelized mode
The procedure for defining a parallelized batch is similar to the one described above, except that this time you need to activate the "Splitting" option and then correctly define the "Number of executors", "Number of groups" and "Maximum number of sub-tasks" parameters (see the image below).
Generally speaking, a CIVA file can be divided into sub-tasks. These sub-tasks are grouped together into clusters, and these clusters are parallelized in the batch process. The number of executors can be thought of as the number of CIVA instances open in parallel. The groups to be processed will be distributed over the defined number of executors.
In this context, a task can be:
- UT: a set of position(s), sequence(s) and/or shot(s)
- CT: a set of position(s)
- Parametric study: the number of sub-tasks will be automatically defined as the number of variation runs divided by the number of group(s)
- For all other techniques, it is not possible to split the CIVA configuration into groups or sub-tasks
As mentioned previously, the efficiency of parallelization will depend on the level of auto-parallelization of the algorithm involved in the calculation.
Parallelization parameters have to be defined manually, and there are no optimal default values that are valid for all cases, as this depends very much on the machine configuration used and the type of calculation launched.
However, suggested best practices include to:
- Check processor activity during a direct calculation:
- If processor activity varies greatly and the processor is not running at 100%, batch parallelization can be effective
- On the other hand, if the processor is stable and already running at 100%, the contribution of batch parallelization will be less significant
- Start with a low number of executors and gradually increase it during the calculation, to ensure that the machine's RAM is not saturated
Complete an already computed Monte-Carlo (May 2023)
As a reminder, in CIVA, the calculation of scattered radiation is performed via a Monte-Carlo calculation for which the user must define a number of photons to model. This Monte-Carlo calculation can sometimes take several hours (depending on the complexity of the configuration - thick part or very absorbent material...).
In several versions before CIVA 2023
After having performed a complete simulation (taking into account direct and scattered radiation), it is possible to reuse the Monte-Carlo already calculated for other simulations.
This option allows the user to change one or more parameters of the model (size or position of the defects for example) while keeping the same scattered radiation as during the first calculation.
CIVA will then calculate only the direct radiations and combine them with the scattering obtained from the loaded Monte-Carlo file. The new calculation will be completed in a few seconds / minutes instead of several hours.
From now on, to use this option, you have to select the drop-down list in the Monte-Carlo options, and click on "Import Monte-Carlo computation".
As a reminder, this option only works in the same size and resolution for the detector and the same source spectrum.
Since CIVA 2023
A new option is available: the "Complete Monte-Carlo" option. This option allows the user, if they think the Monte-Carlo calculation has not converged (not enough photons), to restart another Monte-Carlo calculation using the photons already calculated. No need to restart the full simulation from scratch!
For example, if the initial calculation contains 80E09 photons and you want to model 100E09 photons, you will only have to calculate 20E09 photons.
Definition of an "FE grid" flaw (March 2023)
Before drawing the profile of this defect from the grid editor, it is necessary to define the "context", in order to know if this defect will be considered as embedded in the part or "border", i.e. outer or inner flaw (and therefore if the geometry of the part will be partially included in the finite element calculation area).
It is then necessary to enter the dimensions of the 3D zone in which the defect will be created (this zone must include all the defect(s) accounted for: the defect can be smaller than the zone, its extrusion will be of the dimension of this one. The user may also define small disturbances to be applied to the profiles drawn).
Predefinition of the grid and of the FE flaw
The next step consists in drawing the different profiles of the defect(s). You must therefore enter the editor (Edit the grid sketch) and draw the relevant profile segment by segment (from predefined "vertex", see screenshot below). The grid is initialized with a red line in the center, which corresponds to a planar defect of the same height as the zone. We recommend starting from this predefined flaw. By clicking on one of the edges of this red segment (defect), a blue dot appears. It is then possible to modify the coordinates either with the mouse or by entering its coordinates in the "vertex selection" window.
Default FE grid
In order to modify the size of the defect, its shape, to add other defects or even to modify the shape of the grid, it is necessary to add lines (or segments). To add lines, position your mouse on a gray line or an already existing defect segment (red), and right click on it. Once you have created several nodes, you can add the segments (red) that will define the shape of your defect by clicking on the gray line generated between two nodes. This line will then turn red.
Note 1: You can also divide a red segment by clicking (left mouse button) on the line between the two vertices defining this segment. A new vertex will appear. All you have to do is double click on the unwanted segment, which will turn gray again.
Note 2: If you have chosen an outer or inner breaking notch, you can also modify the profile of the grid, which will generate the creation of a complex profile of your part for which the calculations will be carried out with the FE models of CIVA.
To remove a gray line, click on the "x" that appears just below (on the edge of the grid).
We hope that these elements will help you define your "FE interaction zone" defects.
You will find more information in the CIVA user manual.
Creation of a complex flaw with a locally complex background
Automation of files analysis with associated templates (January 2023)
The first level of data analysis automation in CIVA Analysis is the "Template". It allows you to record a set of actions to be performed on a file. You can watch our video to understand how to use a Template.
The second level of automation available in CIVA Analysis (or CIVA UT) is a "batch" mode, which allows you to automatically load as many files as necessary in CIVA, and to apply a given Template to them. Doing this is very simple:
- An Excel file named "AutoRun.csv" must be defined and located at the root of CIVA Analysis (or CIVA UT). This file must contain two columns: the first one gives the complete path of the file to be loaded including its full name until the complete extension, the second one gives the name of the Template to be applied (without the extension). The screenshot below gives an example. Note that you can have as many files as you want, and each one can have a different Template.
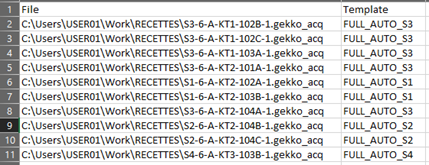
- All that is left to do is to execute the "Go_Auto_UTAna.bat" file (see image below) which is located at the root of CIVA Analysis (or CIVA UT). The analysis will be launched automatically for all the files, and the various files will be saved with the application of the requested Template.
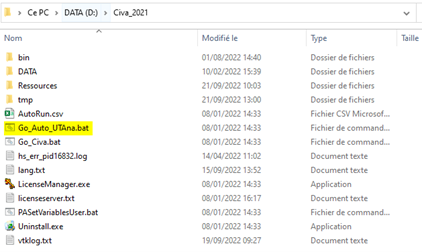
Don't hesitate to use this feature extensively, it should save you a lot of time!
Optimize memory settings for CIVA (September 2022)
This maximum capacity can be modified in two different places on your computer:
- If the encountered limitations deal with the Java process of CIVA, you can modify the default memory size indicated in the set_mem.bat file available in $CIVA_ROOT$\bin\set_mem.bat and increase the indicated memory in MegaBytes. This also enables you to enhance the capacities of CIVA UT Analysis in terms of acquisition files loading and management.
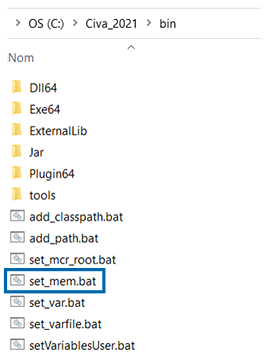
- If the limitations deal with the computation kernel, this has to be modified in your Windows OS properties: System properties / Advanced System Properties / Performances. Then, you have to increase the size of the "exchange file" in the "Virtual Memory" menu. Be careful, as this may also downgrade computation speed.
Superimposition of time signal curves in CIVA TT (July 2022)

In an analysis page, it is necessary to display:
- The thermogram, in order to position the cursors at the different areas of interest to be analyzed.
- As many "Time Signal" images as areas to be analyzed.
The methodology for superimposing the curves is as follows:
- Position the cursor in the first area of interest (e.g., non-defective area).
- Select the time signal image, and use the "Cursor connection" tool so that the view is no longer synchronized with the cursors. The curve will then be "frozen" for the initial cursor position in the thermogram.
- Position the cursor at the new area of interest (e.g., first flaw on the left).
- Desynchronize the time signal image in order to freeze this second curve at the new cursor position. Then, drag and drop from the curve to the previous image in order to compare both time signals by superimposition.
- Repeat these steps for each area of interest.
Parametric studies in CIVA (May 2022)
The design of a parametric study (available for all the NDE techniques modeled in CIVA) starts with the definition and simulation of a nominal configuration of interest. Once this file is defined and computed, the user can go to the "Parametric study" tile from CIVA Desk, and initiate the parametric study by loading the nominal case as reference. A new configuration of *.var extension is then automatically created by CIVA, and the user has the possibility to select, using a right-click, any numerical parameter available in CIVA GUI to include it in the design of experiments of the parametric study.
Definition of a parametric study in CIVA and selection of parameters in variation
In the "Variation" tab, the user can then define the design of variations of the studied parameters depending on different sampling methods: deterministic distributions (for example with linear or logarithmic spacings, following a given statistical law, or a manual draw), random distributions based on various statistical laws, or a parameter distribution ruled by a formula. Regarding the analysis, a data post-processing (calibration, signal processing, etc.) can also be applied to the simulated results of each combination of parameters. Moreover, various extraction features are available, in order to evaluate the impact of the parameters set on a given analysis criterion, for example the maximal amplitude of a defect signal, or even custom criteria which can be specified by a Python script (available with the "CIVA Script" feature).
Definition of the variations' design for the studied parameters using different tools
Once the parametric study is computed, the user can access to each individual simulation results for each studied parameters set (if asked before computation), and to curves and images allowing to visualize the influence of the studied parameters on the defined analysis criteria.
Visualization of the individual simulated results and of the impact of the parameters on the observed analysis criteria
Before or after computations, the user can also benefit from advanced features for parameters sampling and results interpolation (metamodel), in order to predict continuous variations of the analyzed output outside the computed parameters values (between min and max bounds initially defined by the user). These advanced features allow to predict the influence of the studied parameters on the analysis criteria very easily and efficiently, without having to simulate every combination of parameters values (which can become very time-consuming depending on the number of parameters studied). Such features also give access to sensitivity analysis tools, which can be very useful to highlight the most influential parameters on the analyzed output, and they can also be very valuable for reliability studies (POD curves, search for the "worst case" scenario, etc.) and/or optimization work of the simulated END method.
Illustration of advanced features for sampling, interpolation, and sensitivity analysis using metamodels
Do not hesitate to play with these very effective features to carry out your parametric studies in CIVA! We remain at your disposal in case of any question through CIVA support, and we also provide practical exercises about these specific features during our CIVA training sessions and "Reliability in NDE" training course.
Undo (January 2022)
By default, CIVA saves the last four undoable actions (except tabs or elements specific to parametric studies and POD). You can modify the number of allowed "undo" from the CIVA preferences.
"Adjacent configurations" option for POD computations (July 2021)
A POD curve is usually associated with one acquisition channel. But sometimes, it can also be relevant to plot POD curves considering inspection data coming from several channels, if these sensors are associated to detect the same range of defects in the specimen inspection. It is also possible to do that in CIVA thanks to the "Adjacent Configurations" option available since CIVA 2020.
Let's take the example of a weld UT inspection illustrated by the image below. A first channel ("blue sensor") aims at inspecting the volume of the weld on the inner side of the pipe, while another channel targets more the Heat Affected Zone.
Weld UT inspecion example
Of course, if you want to compute the Probability of Detection of longitudinal cracks located in the inner volume of the weld, you first have to consider the "dedicated" channel. But it can be also relevant to take into account the "neighbour" channel that may detect cracks that could be missed by the initial channel.
POD Panel
To do that, you first have to define the POD simulation model of the "dedicated" channel and the different flaw sizes and variable parameters you want to consider. Then, you just have to associate the neighbour channel(s), by loading the relevant CIVA configuration(s) in the "Add Adjacent Configurations" menu available in the "Options" tab of the POD panel. Then, CIVA will apply the POD computation scenario for both probes, and will take into account the maximum signal obtained between the 2 channels for each defect in the final POD curve.
In this case, the first POD curve was obtained when considering only the "dedicated" channel. The famous POD criterion a90/95 (the defect size from which you have 90% of Probability of Detection with 95% confidence) was evaluated at 1.66mm. On the second curve, the adjacent channel "C3" has been included in the POD study. Since many "hits" are obtained with this new channel (some of them are displayed with red crosses on the graph below), the resulting a90/95 is now evaluated at 1.26mm.
Initial POD curve
POD curve including the "adjacent channel"
Mesh display and optimization of CIVA ET axisymmetric models (May 2021)
Automatic and fast computation of TCG calibration curves for inspection configuration with single and multi-elements probes (March 2021)
Automatic computation of TCG calibration from the "Simulation settings > Calibration" panel
Once the calibration is defined and computed, the user can run the computation of the studied inspection configuration, and the output results will be automatically calibrated considering the computed TCG data. The figure below displays an application example of CIVA TCG computation, used for a 16 elements probe inspecting a calibration block with 9 side-drilled holes of 2mm diameter located at depths: 10mm, 20mm, 30mm, 40mm, 50mm, 60mm, 70mm, 80mm, 90mm.
In this simulation, the probe acquisition settings define a sectorial scanning from 55° to 65° with 1° step, and the computed TCG settings are identical to the simulated inspection configuration. By comparing the results obtained with and without computed TCG calibration option, the simulated SDH responses are well rectified to 0dB with computed TCG calibration for all the shots of the acquisition sequence and all the defect depths.
Simulation of a calibration block with a 16 elements linear probe with and without TCG simulated calibration
During the calibration pre-computation, CIVA automates beam computations (with 2D or 3D options) in ideal/simplified configurations, in order to build in almost real-time and with reasonable accuracy the calibration TCG curves to use for inspection configuration simulation. Considering the simplifications, such automatic calibration computation can be less accurate compared to the exact calibration procedure simulation, when the ultrasonic beam is steered compared to its geometrical rays of main energy, as illustrated in this example, with a maximal calibration error of 1.2 dB for the closest depths to the entry surface (near field) and the highest refracted angles (beam deviation). Such errors appears reasonable considering the computation performances of such calibration tools, allowing you to compute the TCG data of a phased-array probe with large numbers of acquisition sequences and side-drilled hole depths in less than a minute with a conventional computer in most complex application cases.
Please note that the user can also extract the TCG calibration data of single and multi-element probes in a text file to understand its structure, potentially modify its calibration values, and load the new calibration file as simulation results post-processing calibration of an inspection configuration.
Beam calculation: Max beam only (September 2020)
This feature is particularly useful for simulations with a large computation zone and/or many modes to consider.
When this option is selected, the results include only the maximum amplitude value and the corresponding time of flight for each point in the computation zone. However, it is no longer possible to post-process the results to modify, for example, the reference signal or the computation options.
The “Max beam only” feature is accessible from the “Simulation settings” menu, in the “Storage options” section (see image below).
The settings presented above are used to compute the beam image in Transmission/Reception. Two other options are available to compute the field in Transmission and/or in Reception.
The image below presents a comparison between a default beam computation result (on the left) and a result with the setting described above (on the right) for a transducer generating 45° transversal waves in simple block made of steel.
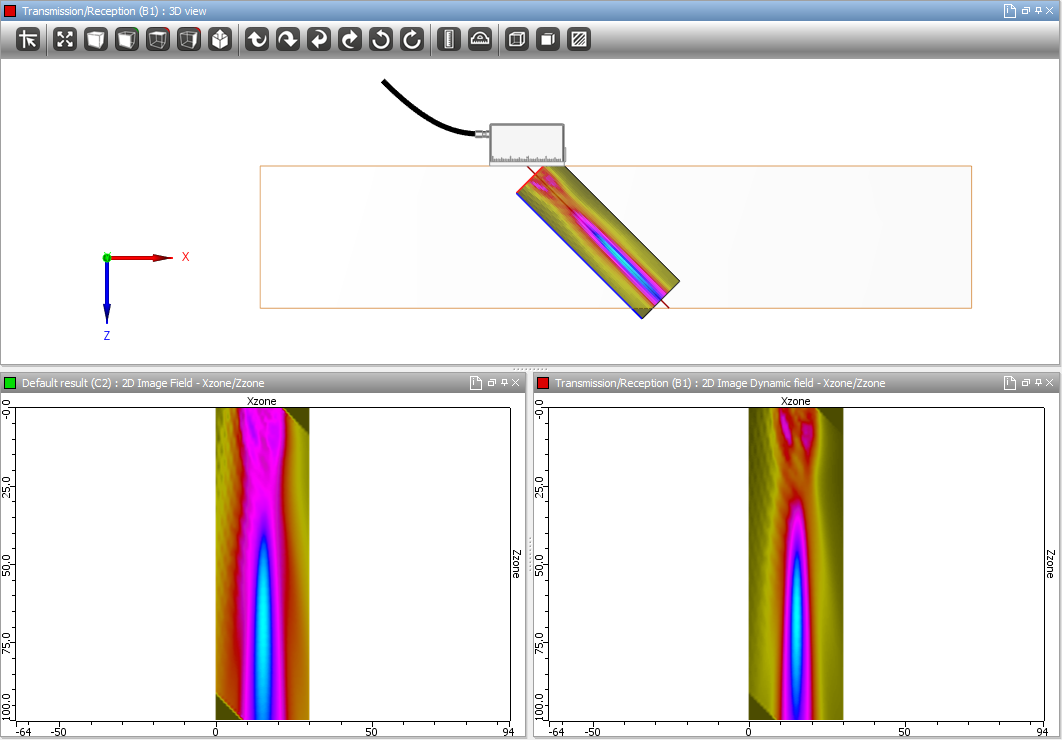
Comparison of beam images
Left: Default beam computation
Right: Beam computation with "Max beam only" selected and image in Transmission/Reception
From the default result (image above on the left), an additional post-processing step must be performed to obtain the beam in Transmission/Reception. In addition to the extra time to complete this step, it would also increase the total size of the result file.
In the case of a phased-array transducer, the “cumulated” and “dynamic” images are available after computation, but post-processing for example to modify delay laws is no longer possible.
The image below illustrates the result that would be obtained with an angular scanning focusing. Dynamics images are calibrated from the shot generating the maximum amplitude.
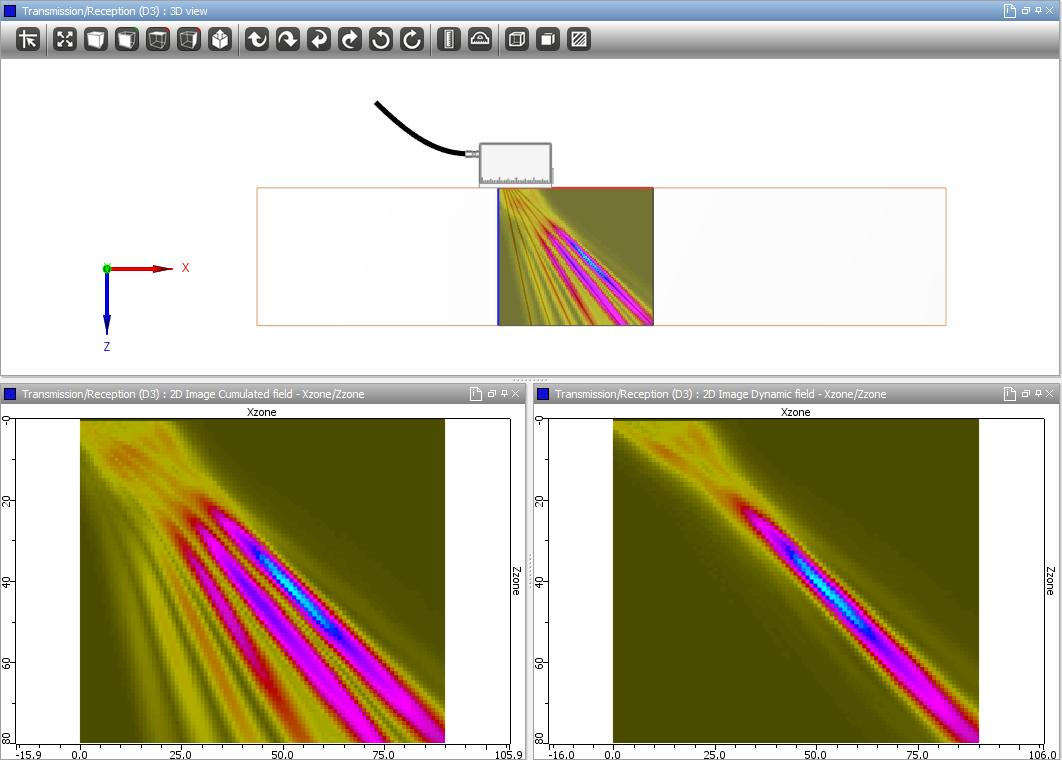
Results with a phased-array probe and the "Max beam only" option
Left: Cumulated image
Right: Dynamic image
Optimization of calculation times in CIVA CT:
Import of Monte-Carlo calculation results with a variable step (July 2020)
This option allows to import Monte-Carlo calculation results with a variable positioning step.
It is thus possible to refine the calculation of the scattered radiation on irregular regions or strong variations in thickness and, conversely, to widen the step on flat or quasi-planar areas where the thickness is constant (see image below).
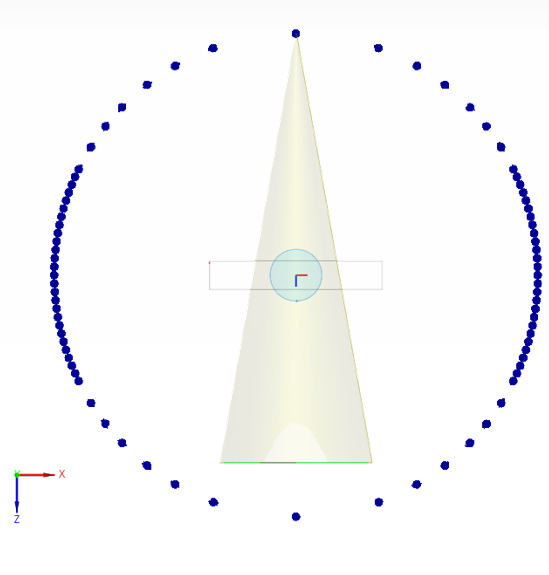
Illustration of the step between two Monte-Carlo calculations for a tomographic configuration of a flat specimen.
Two import modes are proposed via a drop-down menu:
- File in CSV format: the description of the imports to be carried out is made in a CSV file,
- Manual: the description of the imports to be made is done directly in the CIVA interface.
Import CSV file
N.B.: The CSV file and the CIVA configurations containing the scattered results (Monte-Carlo calculations) to be imported must be in the same folder.
The CSV file must contain three columns separated by semicolons, and as many lines as there are positions.
The content of each line is as follows:
- First column: index (tomographic position). The initial value is 1.
- Second column: CIVA tomographic or radiographic configuration to be considered (*.civa). Only the name of the configuration is to be specified (since all the configurations are in the same directory as the CSV file).
- Third column: position to be considered for the reloading of the scattered radiation calculation. If the loaded configuration is a radiographic configuration (1 position), do not put anything. If the loaded configuration is a tomographic configuration (several positions), fill in the position to be loaded.
An example of a *.csv file is shown below:
Lines 1 and 2: The configuration "Config_pos_0.civa" is a radiographic configuration, so there is no need to enter the position to be loaded in column 3.
Lines 3 and 4: The configuration "Config_pos_22-5_to_42-5.civa" is a tomographic configuration. In that case, it is the first position of the configuration "Config_pos_22-5_to_42-5.civa" that has to be loaded.
For lines 5 and 6, it is the second position of the same CIVA file that must be reloaded.
“Manual” import
The description of the imports is made in the CIVA interface through a table with the following fields:
- Index: number of the import. The increment is done automatically when a new line is added by the user (using the + symbol).
- Nb of positions: number of successive tomographic positions for which the imported diffusion will be used.
- File name: CIVA configuration in which the previously calculated diffusion will be imported. The window allowing for the selection of the configuration is accessible by clicking in the box. It is not necessary for all configurations to be in the same folder (absolute paths are specified).
- Position number in scatter file: position to be considered for the scatter in the CIVA configuration specified in the previous column (if tomographic configuration).
Mode identification in CIVA GWT (March 2020)
To do this, you have to go in the "Toolbox" (tab "View Options") and untick the display of All modes with the same color. Then, assign a different color, and display the modes that contribute to the echo (as shown below).
In addition, the mode identification can also rely on other elements:
- The energy emission and sensitivity at reception data from the dispersion curves enable you to identify the modes that are actually sensitive in transmission and reception.
- For each of the strong modes, the time of flight from the probe to the reflector can be estimated with the energy velocity dispersion curve.
Optimization of calculation time in CIVA RT/CT:
Detector degradation for a Monte-Carlo calculation (January 2020)
It is now possible to degrade the resolution of the detector during the Monte-Carlo calculation and to merge this result with the result obtained by the Beer-Lambert calculation (contribution of direct radiation) for which the detector is not degraded (and thus is defined as entered by the user in the detector panel).
The value to be entered is a percentage of degradation.
This functionality is accessible from the "Options / Simulations" menu, Monte-Carlo section. The desired percentage of degradation is to be entered in the box "Detector degradation of total pixels number".
The percentage of degradation relates to the total number of pixels and is carried out at constant detector size. It therefore results in the pixels being artificially "magnified".
For example, if a resolution degradation of 75% is applied to a detector containing 2E06 pixels and measuring 10 cm × 20 cm, the Monte Carlo calculation will be performed on 0.25 × 2E06 = 5E05 pixels, and the detector will still measure 10 cm × 20 cm. Pixels for which the Monte Carlo has not been calculated will take the value of the nearest neighbour.
This degradation of the detector resolution has an impact on the number of photons to be modelled, and thus on the resolution time of the Monte Carlo calculation (i.e. the fewer pixels on the detector, the lower the number of photons necessary to ensure the convergence of the Monte Carlo calculation is).
When the percentage of degradation applied to the detector is too high, the "Combined Energy Scattered" images can take on an unusual appearance (inhomogeneities) (see image below). It is therefore important to check this image to ensure that the degradation factor applied is relevant.
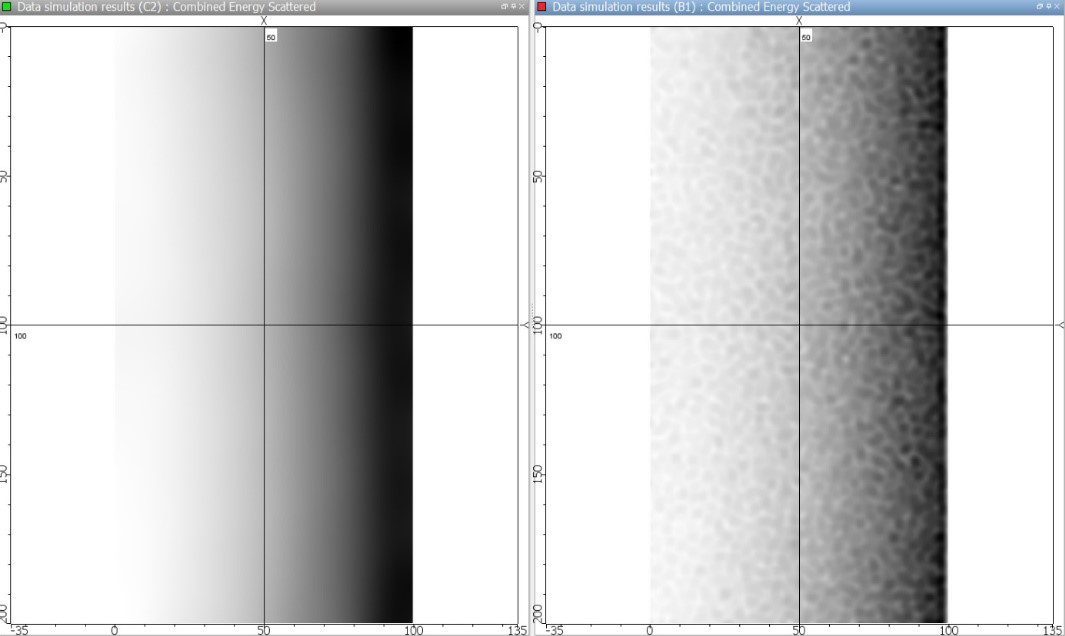
"Combined Energy Scattered" images for two degradations of detector.
Left: Degradation of 0% (detector without degradation). Right: Degradation of 95% (detector too degraded).
Save and load TFM reconstruction zone (September 2018)
Import acquisition Data (July 2018)
You probably know that CIVA can directly load M2M Phased-Array systems data files (MultiX, Gekko, etc.) as well as Olympus ones (opd, oud, rtd) in their native formats.
But CIVA is very flexible, and also offers the possibility to read other types of data through "PlugIn" solutions.
There are two methods that you can follow:
- You can first export your acquisition data into a text file, right from your acquisition or analysis software. Then you will use the "CIVA files (txt)" PlugIn to import this text file inside CIVA.
- Or you directly load the native data file inside CIVA.
To import text files
The process is quite fast in this case, as this PlugIn is already fully defined. You just have to organize your data file so that this plugin can properly read and load it in CIVA.
This PlugIn is called ImportUTCIVA and is available in your CIVA folder under $CIVAROOT (for instance C:\Civa_2017)\bin\PlugIn64\importUTCiva.plugin)
The document "Import plugin UT CIVA.pdf" describes the way data should be organized.
It is basically a simple header, and then a classification of temporal signals data in columns following the so-called "IBST" order (I: Increment; B: Scanning; S: Sequence (in case of electronic scan); T: Shot (in case of multiple focal laws, such as sector scan for instance)).
Once your file is properly set, just call it from the CIVA file manager or the desk through the load button.
To import native data files
This PlugIn is called ImportUTDataFile. In that case, some more work has to be done thanks to the Development kit provided.
Developing the ImportUTDataFile PlugIn consists in:
- Developing a DLL (Dynamic Link Library): The role of this DLL is to provide all information to convert your UT Data Format to a CIVA native format. CIVA provides a full development environment compatible with Visual C++.
- Setting two XML configuration files (*.xml description of input and *.xml description of PlugIn), to help CIVA interpret your DLL.
- Setting a ".bat" file that will contain some runtime settings, and will constitute the PlugIn launcher.
The documentation, development kit and an example are available in your CIVA folder $CIVAROOT (for instance C:\Civa_2017)\bin\PlugIn64\importUTDataFile)
You can start your implementation by using the example available, "SampleImportPlugInDll.plugin", and then progressively adapt it to your own files.
You can contact us to help you in that process, either through the support service if you handle this development but that you have specific questions, or through a full consulting service if you wish us to develop the PlugIn for you.
Detectability criteria (May 2018)
The first one, "Pseudo Rose", is inspired from the work of Albert Rose, and is adapted for roughly circular flaws. The second one, "Ellipse", was developed for silver film; and the third one, "Fushia", is based on the "Pseudo Rose" criterion and is adapted for elongated defects.
To use those criteria, don’t forget to tick the "Simulate images without flaws" option from the "Options" menu, "Computing" tab before launching your calculation.
In the analysis page, select the "Response detector noise" image, then select the "Detectability" menu (bottom of the analysis window).
Then click on the "+" button and select an area of measure.
By default, the Rose criterion will be displayed. This can be changed by clicking in the "Detectability" menu.
With the Rose criterion, a defect is considered as detected when it has a value above 7.
You will find more information about those criteria in articles available on our website and in the CIVA user manual.
Probes library (March 2018)
This library is available in the "Probe" panel, in the "Library" tab on the top left of the panel, by clicking on "Import from manufacturer library":
The probe is then directly imported in CIVA:
Use Bookmarks to browse your files very easily (January 2018)
It is possible in CIVA to define “Bookmark” directories, directly accessible from the "Desk" (CIVA home page). It's very simple, just click on the icon:

Then, by using the small "+" icon located at the top right of the screen, you just have to define as many Bookmarks as you want. They will appear directly on the Desk's right hand side, on the right of the file history (recently uploaded files). All you have to do is to click on one of the folders to directly access the simulation files it contains.
Apply a “Distance Amplitude Correction” by signal processing (November 2017)
To do that, do a right-click on the data in the CIVA manager, then select "Edit VAR parameters".
In the new page, define a DAC "signal processing", fill the corresponding chart in (time and gains), then click on "New". It is also possible to define a reference amplitude (for example, the maximum amplitude of the DAC in "points", arbitrary unit in CIVA) in order to obtain the results directly in dB.
Time and gains data would have been obtained from a previous simulation with calibration reflectors at different depths.
This signal processing can be saved also in this window, don’t forget this option which will allow you to load it in one click in a future case !
Once these steps are done, a new page appears in which the data are shown in dB and by taking into account the DAC.
Define your detector and reload it later in others configurations (September 2017)
Once you have filled in all the information in the selected panel (detector in that case), just select the "File" menu, then "Save" on the top left side of the panel.
By doing this, you will save the geometry of the detector, but also the material of the sensitive layer, and the filters if you have defined any.
When you will define the same detector for another configuration, just load the *.xml file containing all the data from the same place with the "Open" menu. Don’t spend any more time modeling it!
This feature is also available for other panels (component, flaw, IQI...).
Modes list definition in UT beam computation (July 2017)
This setting can be accessed from the "Simulation settings" panel under the "Options" tab. By default, only the direct mode will be computed by CIVA. This corresponds to the direct path of the ultrasonic beam.
By activating the “Specimen’s boundary reflection” option, it becomes possible to define the ultrasonic path to be taken into account in the computation by defining the number of reflections.
It is also possible to check and specify the modes that will be computed by CIVA by selecting the "Specify mode list" option. The list of computed modes now appears in the interface.
Using the right-click on a particular mode of this list, it is possible to remove a mode from the computation.
The modes list can also be imported from a text file. To do this, the file must contain, on each line, the mode to be taken into account. The nomenclature of the modes is shown in the example below (example with T wave and reflections on the backwall and the surface). There is no special header on this file.
Then, this modes list can be imported using the “Load” command.
3D CAD / DXF Export (May 2017)
To simplify the transition from an existing 3D CAD to a 2D CAD, it is not necessary to draw the specimen in the CAD editor of CIVA.
Simply display a section view of the 3D CAD, right click on the specimen, and select "Component", "Export Profile to .dxf".
The *.dxf profile that has been saved can then be imported into CIVA. Before launching calculations, you must reassign the right colors to the specimen surfaces, since all segments of the saved profile are in comment after the export.
UT Analysis operators (March 2017)
How to display the corner echo at its correct location (January 2017)
What happens now if the flaw is an outer breaking notch, and a “full skip” option is required to correctly model the configuration?
The figure below represents an inspection with a T45° probe angle with an outer breaking notch:
As visible below, the reconstructed B-Scan in the 3D view displays by default the main corner echo of the flaw outside the specimen.
From the tool box, in the Options tab and in Visualization properties, by selecting the number of reflections, raypaths can be reflected after reaching the backwall or the surface. The true view in this case is the sum of a direct and a reflected image.
It is then possible to choose the number of skips wanted to account for in the image, and simply click on “OK” to apply. A reconstruction with one reflection is displayed below.
Multiple skips reflection is also possible with a large number of reflections.
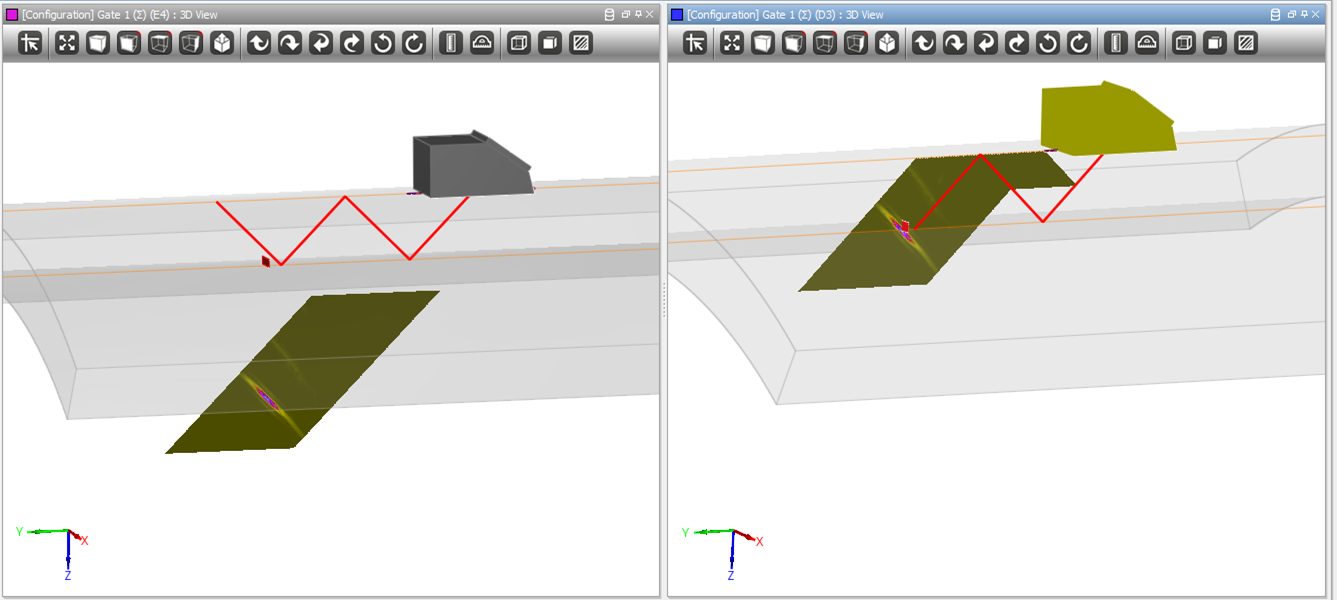
Ray beam coverage in CIVA 2016 (November 2016)
improve the reconstructed view in particular cases (September 2016)
These behaviors are due to the fact that data is reconstructed along a path based on the central ray and, in some cases, this ray can be locally affected (e.g. : particular incidence compared to an interface, impact point of the ray on a junction between several interfaces, etc.).
In order to bypass this problem, the "Smoothing" option is very useful. It is located in the toolbox at the bottom of the screen.
Compared to the left view of the second image above, the use of the "Smoothing" option gives a much better reconstructed view.
Eddy Current Array Probes (July 2016)
Indeed, it is possible to define this kind of sensor using an array probe editor, available by selecting the "Array probe" type.
For this kind of probes, one or more layers can be defined. Each layer can contain a different number of elements, and a different type of coil. The editor makes it possible to define all these parameters in a few clicks.
Wiring can be defined in several ways, such as "All elements on the same cable" or "One element by cable", or even in a more complex way thanks to an expert mode giving access to a wiring editor.
The acquisition channels (common functions, separated functions) can be defined very easily by describing a basic pattern gathering the active coils together and their role (respectively driver coil, Pick-up coil, Driver-Pick-up). They will appear in the editor with a clearly identifiable color (respectively red, blue and pink). The electronic scanning can be defined on the whole sensor with a sequence editor (automatic or manual path). Several channels can be defined in a single simulation.
A mechanical scanning can be associated with the electronic trajectory.
The C-Scans enabling the visualization of the different channels are then defined.
One C-Scan per channel is available, other C-Scans can be added by the user before running the solving process.
The results corresponding to the defined C-Scans are available after the solving process.
Regarding the tube inspections, the "X-probe like" type of array probes can be defined. For this type of probe, the settings is predefined in the interface.
The probe can cover the whole tube's circumference by selecting the 360° option, or only a part of the tube without this option.
The options available in this interface enable the user to quickly define the properties of the probe, for example:
- The general properties of the array probe (number of rings, number of elements per ring, distance between the rings, lift-off, ...).
- Dimension of the coils which compose the probe.
- 3 patterns as well as the electronic scanning are defined automatically and can be seen from this dedicated interface (driving coil in red, pick-up coil in blue).
A mechanical scanning can also be associated with this array probe.
By default, two C-Scans are defined before the solving. Both channels can be analysed after the computation: one corresponds to an axial detection and includes both axial patterns, and the other corresponds to a transverse detection. If necessary, other C-Scans can be added by the user. After computation, the results are available for the different C-Scans which have been defined before running the solving process.
Subtraction (May 2016)
Clicking on this icon opens a post-processing window, with the "Envelope" processing type defined by default.
To access to the other processing types, click on "Envelope", and the whole list will appear.
Select "Subtraction" and the appropriate window opens.
Now, as in the previous CIVA versions, you can directly delimit the signal to remove on the reference signal A-scan. The output signal A-scan will be interactively modified. Then click on “Apply” and then on “New” to open the new analysis window with the output signal A-scan.
In the example below, the lateral wave is removed from a TOFD inspection A-scan.
It is also possible to load a reference signal in a .txt format and apply the subtraction of the whole reference signal, or only a part of it, by modifying the "min Time" and "max Time".
optimize an RT configuration (March 2016)
First of all, a Region Of Interest (ROI) can be defined.
To define it, select “Use ROI” from the Options panel / Detector tab.
The region of interest is a small rectangular region within the film which is sub sampled to obtain a finer resolution. Select the “Up scaling” factor in the drop-down list. By selecting a refinement factor of 2, the surface of each pixel in this zone will be refined by a factor of 4, which means a significant increase in convergence rate.
Then you have to define:
- X max
- X min
- Y max
- Y min
The ROI appears on the detector in the 3D view.
Secondly, options of the Monte-Carlo calculation available from the Options panel / Computing tab can be modified to reduce the time of calculation.
Cut energy: By ticking this option and keying-in a value of energy, photons with incident energy lower than this given value will be automatically killed. This option reduces the computation time.
Cut according to order scattering: By default, CIVA can simulate up to 10 orders of scattering for a given photon. This option allows you to stop the propagation of the photon if it has reached the number of order scattering defined.
Import Monte-Carlo computation: For more information about this option, look at the tip “RELOAD AN ALREADY COMPUTED MONTE-CARLO” available below.
Thirdly, it is possible to optimize the utilization of the computer for the calculation, by modifying the Preferences (top left of the CIVA window).
A Monte-Carlo calculation is sequenced in multiple cycles, for which it is possible to define the number of photons considered. By default, a cycle is composed of 100,000 photons. By increasing this value slightly, it is possible to reduce the number of cycles that will be calculated for a given number of photons to be simulate, and thus to save time. This option is available from the X-ray tab of the Preferences.
Reduce the memory size of a CT configuration
Combining BL and Monte-Carlo calculations generates lot of images that are not always useful for the user. When the user doesn’t need to see those results, it is possible to select the “Keep only the Detector response data” option. By doing so, only images from “Response detector” or “Optical density” will be stored, and the memory size of the configuration will be significantly reduced (especially for CT configurations, for which results can exceed 100 Go of memory).
How to display and calibrate variation curves in dB or % (January 2016)
It is possible to calibrate the curve according to a reference chosen by the user in order to display it in dB or %. To do so, in the CIVA manager, right-click on the result and edit the variation parameters.
A new window opens where you can tick the option "calibrate". Then, you have the possibility to choose between a calibration in dB or in % (linear scale). According to the chosen calibration scale, you have to specify the reference amplitude (for dB scale) and the corresponding value (for linear scale). In the example below, the reference amplitude corresponds to the highest Amax value in CIVA points, and the corresponding value relates to the percentage it will be associated with after calibration.
Click on the "New" button at the bottom of the window. The calibrated result is then displayed in a new window and appears in the CIVA manager.
Photons Count Estimator (November 2015)
This number of photons to be modelled depends mainly of the following parameters:
- The X-Ray (or gamma Ray) energy source
- The inspected material
- The thickness of the material
Since CIVA 2015, an estimator of the minimum number of photons to be simulated has been included, to help the user in preparing the configuration. This option has been developed to choose an adapted number of photons for each configuration.
To illustrate how this tool is operating and useful, we present here an example of a simulation of a pipe inspection with the so-called “ellipse” technique:
With an insufficient number of Monte-Carlo photons defined in the configuration and performed without this estimator tool, the simulation provides the result displayed hereafter:
We can clearly see that the result is not satisfactory, as most of the pixels on the detector were not impacted by any photons. It is nearly impossible to recognize the irradiated object: not enough Monte-Carlo photons have been simulated to converge towards a correct result. Without this estimator tool it is therefore necessary to relaunch as many simulations as needed increasing the number of photons to be simulated till a relevant result is achieved.
A click on the “Estimation” button launches a quick Monte-Carlo simulation. At the end of this simulation, CIVA proposes in the GUI a number of photons to consider in order to perform a correct simulation.
Let’s run the same configuration with the number provided by the “Estimator”. The result is displayed below:
This time, we can clearly see that we obtained the expected result. The irradiated object is clearly seen, as well as the ellipse.
This tool is really beneficial to help the user in defining the number of minimum requested photons to get an accurate result.
We really hope you will enjoy this new capability of CIVA 2015!
"Auto" mode in frequency post-processing (September 2015)
Inches and millimeters (July 2015)
Thus, since CIVA 2015, the CIVA Graphical User Interface allows keying in any numerical parameter in inches instead of mm. And this is very easy to do, once you know the trick!
As you can see on the screenshot hereafter, keying in a pipe diameter in inches just requires to use the “i” letter just after the expected value; e.g. you can key in “20i” to set a 20 inches OD tube. When validating the value by pressing “Enter”, CIVA automatically makes the conversion and displays the value in mm. A tooltip is visible when moving the mouse on the numerical value, giving you at any moment the value you defined in inches.
The GUI is now even more powerful, you can also use mathematical common operators (summation ”+”, substraction “-“, etc.) and other common symbols such as the “fraction” one, which can be very useful when defining the size of the probe crystal as illustrated on the next screenshot.
We really hope you will enjoy this new capability of CIVA 2015!
ET Calibration (May 2015)
CIVA includes the tools to define such calibration reference. This Tip focuses on how to calibrate a result in the Eddy Current module of CIVA.
The first step is to describe the reference flaw (as a calibration mock-up) and to simulate its signal in order to compute the relevant calibration gain and phase rotation coefficients to create the reference signal defined in the procedure. Once done, this coefficient will be used to calibrate all simulation works that the user wishes to relate to this reference.
To do that, just follow the steps described in our video.
Assign a material (March 2015)
Adjust 2D CAD elements (January 2015)
It is sometimes difficult to link segments and circles arcs since the exact coordinates of the connection point are generally unknown. The "Adjust" feature of the 2D CAD editor enables the user to easily connect the elements.
Cursor Modes in Eddy Currents (November 2014)
Simple mode cursor
This tool can be activated from the "Image tools" menu (2nd icon, cf. image below). It enables to obtain the values measured from the origin of the impedance plane.
Values at the different positions of the probe can be obtained by moving the cursor which controls the probe position (from the 3D view, or with the vertical cursor of one of the analysis curves), these values are given in the "Amplitude" part of the tool bar. The maximum amplitude can be obtained by moving manually the cursor at the position corresponding to the maximum amplitude of the signal in the impedance plane.
Double cursor mode
Another cursor mode is also available in CIVA, the double cursor mode. It enables to automatically obtain the maximum amplitude of a signal. This mode can be activated from the "Image tools" menu (the 1st icon allows you to switch between single cursor and double cursor mode). In this mode, the user can select two probe positions thanks to two cursors; the maximum amplitude of the signal between the cursors and its phase are then automatically given in the "Measurement" part of the tool bar.
Two measurement modes can be defined under "Parameters" tab:
- With the "Absolute" measurement mode, the measured amplitude corresponds to the amplitude of the signal from the origin of the impedance plane, as for the simple mode cursor.
- With the "Relative" measurement mode, which corresponds to a measure in differential mode, the given amplitude corresponds to the peak to peak amplitude of the signal.
CAD Export (September 2014)
Reconstruction and mirror effect on B-scans for CIVA 11 (July 2014)
You may need to change the reconstruction for a better understanding of the results. CIVA 11 proposes a new way to realize this process.
The “Propagation mode” option allows reconstructing the data according to the T wave mode (red ray) or the L wave mode (green ray). Thus, the echoes are positioned in the reconstructed view according to the path and the velocity of the selected mode.
In some cases, typically for inspection configurations after skip on the backwall, to display the results, it may be useful to use a “mirror effect” on the backwall. To do that, tick “Reflection” as shown below.
Inspection of a 2D CAD specimen by the extruded side (May 2014)
By default, the profile extrusion is along the Y axis.
An extrusion along the Z axis enables the simulation of an inspection from the extruded face. To do so, draw all the surfaces of the profile to be extruded in blue (side) or green (backwall). The color should be chosen according to the simulation settings. In the example below, the hole is drawn in green so it is possible to calculate echoes after skips on its surfaces.
How to build a video in the CIVA ATHENA2D module (March 2014)
Move your CIVA soft key onTO another machine: the “Rehost” feature (January 2014)
An SL key is installed on a given machine from a *.C2V file, which includes the software footprint of this computer. But once installed on this machine, the licence is still movable, and can be transferred with a few clicks: this is the “Rehost” process, described below. Once the license is transferred, any future update will be done on the new machine currently hosting the license, without the need to reinstall it on the initial machine or to send the footprint file again.
If you know you will change the computer on which you run CIVA, remember to transfer your CIVA license thanks to this operation before leaving your machine!
The Rehost mainly uses the RUS utility, available from the CIVA license manager (“Tools” tab) or from your CIVA installation folder:
[CIVA Installation Directory]\Prerequisites\Sentinel\Vendor\RUSforCIVA11.0_KQCZM.exe
Step 1: Generate an identification file *.Id for the machine that will receive the licence
Go to the recipient machine on which you will move your CIVA license and open the RUS. Go in the “Transfer License” tab, then in the “Save recipient information to” browsing button:
With the browser, select and save a relevant name (machine name for instance) and location for your *.id file then select “Collect and Save information”.
A confirmation window will appear:
In case of a future Rehost operation on this machine, this *.Id file can be re-used. Therefore, think about saving all the *.Id files of your machines in a relevant and centralized way, so that you will not have to do this first step again in the future, and be able to start directly at step 2!
Step 2: Generate the licence transfer file from the machine currently hosting the licence
Go on the computer that currently hosts the active CIVA license, and copy there the *.Id file created at step 1. With the RUS, same tab as before, generate the transfer file by first indicating the location of the *.Id file, and then by defining and saving with the browser a name and a location for the license transfer file *.h2h to be generated. Finally, click on “Generate the license Transfer File”:
A confirmation window will appear, the license is deactivated on the initial machine, and the *.h2h file is created:
This *.h2h file is only valid for one transfer in one direction. It can be deleted afterwards, but be careful not to lose it now, as it holds your CIVA license!
Step 3: Activate the licence on the new machine
On the new machine, copy the *.h2h file and, still from the RUS, apply this *.h2h file in the tab “Apply license file – Apply update”. The license is now active on the new machine!
Data reconstruction comparable to your acquisition image (November 2013)
However, when you make the inspection of the real piece exhibiting the cladding, most acquisition devices or analysis software do not allow you to set the parameters as completely as what you can do in the CIVA model. Thus, the reconstructed image that you get does not take into account the anisotropic cladding, and the positioning of defect indications is wrong. It may be interesting to use CIVA to highlight the difference due to the cladding, and obtain by “degrading” the CIVA model a reconstructed image comparable to what you get on your acquisition system. To do this, simply right-click on the data source of your original file (containing the complete model) and select “Save As.”
You can then reopen the saved file, which is now interpreted by CIVA as an “acquisition” file, in which it is possible to modify the model parameters and apply the new parameters without having to run a new simulation. In our example, we simply modify the material of the cladding to the same material as the rest of the test piece, and press the “Apply” button at the bottom right of the 3D visualization window.
Finally, when you open the reconstructed Bscan image and display it in the 3D view, you get the picture below which no longer reflects the influence of the cladding.
This trick will enable you to be able to easily compare an image obtained during an acquisition with the CIVA reconstructed image under the same conditions, while having done the calculation with a specific model as close as possible to real conditions. This example demonstrates the advantage of this capability. It can be applied in many cases, what is the impact of an inappropriate delay law? A specific geometry not taken into account? An attenuative material or deflection of the beam? We trust you to use this feature and utilize all the benefits from it.
Visualization of ultrasonic propagation (September 2013)
The visualization of the beam propagation is necessary for some configurations, in particular to illustrate some phenomena with CIVA-ATHENA2D. To display it, switch in the data tools from Amax to A(t).
The obtained 2D image depends on the time. Adjust the time cursor of the A-scan to visualize the propagation at different times of flight in the 2D image or the 3D view.
It is also possible to generate a video file by clicking on the dedicated button.
Handling Drag and Drop (July 2013)
To do so, open a new analysis page.
Then click on the first result. The scan explorer displays the available images. The green circle stands for an image already displayed in an analysis page, the red square for an image not yet displayed.
Drag and drop the useful scans into the new analysis page
Now click on another result, you can drag and drop other images. A grey rectangle stands for the future positioning of the dragged image in the page.
You can drag and drop images from as many results as you want.
Each image has a color icon referring to the corresponding result.
Additionally, it is possible to superimpose the curves having the same axes (time, scanning steps, scanning increments…). Click on a curve, drag it over another curve and release it. Use the double cursors for a quick measure of the differences.
Modes identification (May 2013)
To identify the simulated echoes on the Bscan or True Bscan, select them with the selection tool accessible in the data toolbox.
Once the tool is activated, the contour of the zone is drawn with successive clicks. To stop drawing the zone, double-click on the last point of the zone.
The modes and their relative contributions in the formation of the echoes in this zone are displayed as shown on the following image. The name of a mode refers to its path.
After activating this tool again, it is possible to draw multiple mode identification zones. A right-click on a zone allows the user to remove these zones (choice “Remove” or “Remove all”).
Convert zoom to limitation (March 2013)
After zooming in any view that is not a reconstructed view (A-scan, B-scan, C-scan, echodynamic…), the magic button “Convert zoom to limitation” is available from the data tool.
A new dataset appears in the current configuration tree of Civa manager. It is then possible to display the limitation result in a new analysis page.
The limitation parameters are displayed in an additional view on the left of the CIVA window. The values correspond to the limits of the not True view from which the “Convert zoom to limitation” button has been applied.
A red rectangle also displays the limitation in the original B-scan. The limitation can be adjusted by dragging the limits of the rectangle or entering values in the previous window.
For an easier analysis, it is possible to save only the limited data. Then, one can load only the useful information, and for example apply signal processing.
Smooth a C-Scan in CIVA ET (January 2013)
To smooth a C-Scan in CIVA ET, right click on the raw C-Scan then select “Interpolation”. It is different from the smoothing of a field computation image (UT or ET) which is done from the “Image Tools” toolbar on the top of the image.
Then, the C-Scan is duplicated in the current page and, in the toolbox at the bottom of the window, 3 interpolation functions are proposed to the user: Linear, Spline and Cubic (actually Cubic Spline). Cubic Spline algorithm is quite popular as an interpolation function; this choice is sometimes detailed in analysis procedures.
Once the algorithm is selected, the results are interpolated and represent a certain number of points defined by the user along each axis of the C-Scan. The more points you have, the thinner resolution you get. Different results are presented below for a different amount of points.
In addition to the Smoothed C-Scan, CIVA ET creates in the meantime a full set of data in a second analysis page. Therefore, the user can also display the associated curves based on the same interpolation: Impedance plane, X and Y channels, Amplitude and Phase curves.
Ray tracing tool and pencil method (November 2012)
In CIVA UT results, the rays are displayed from the center of the probe to the specimen, according to the local properties at interfaces. For a better understanding of the propagation, it is possible to display a beam of rays.
These tools help to visualize the path of the ultrasonic beam. They are used for the reconstruction of the true scans only.
CIVA models are based on the pencil method, in which matrices take into account the propagation in each medium and at each interface from a source point.
The field radiated by the total aperture of the probe is obtained by a sum of the fields on the different source points constituting the probe. This method is therefore able to compute the time of flight, the polarization and the divergence of the beam.
Reload an already computed Monte-Carlo (September 2012)
In CIVA, the interaction of the photons with the inspected specimen is simulated with a Monte-Carlo method, in which a given number of photons to be simulated must be defined.
The Monte-Carlo computation may take several hours.
After performing a simulation taking into account the direct and scattered radiation, the current version of CIVA allows to re-use the already computed Monte-Carlo for other simulations.
You may need to change the flaw position, dimension, or other parameters.
The “import Monte-Carlo computation” option allows the user to change one or several parameters of the model, and to keep the same scattered radiation than for the first computation.
CIVA will then compute only the direct radiation, and combine it with the scattering gotten from the loaded Monte-Carlo file.
The image below represents a comparison of two simulations with two different sizes of inclusions. The first computation has been simulated with 10E9 photons (5 hours for the computation). In the second one, we loaded the Monte-Carlo from the first result (2 minutes for the computation).
Important notes:
- This tool is only available when keeping the same detector resolution and size.
- When using this tool, the user must be sure that the scattering effect will be the same in the different configurations.
Display several scans in the 3D view (March 2012)
It is possible to do that thanks to the “frozen scan” feature:
The configuration below involves a phased-array UT probe with a linear array. One electronic scanning is operated along the circumferential axis of the tubular specimen, while a mechanical increment is used along the axis. The simulation generates a Bscan image (Electronic Scanning vs. Time), a Dscan image (Increment vs. Time) and a Cscan image (Electronic Scanning vs. Increment):
As an experienced user of CIVA, you already know that a simple drag and drop allows you to display an image in the 3D view. This superimposition of the true scans and the flaws helps the analysis of the different echoes:
But it is also possible to display several Bscans (or Dscans) for several positions. To do this, right click on the first one displayed in the 3D view, then select “Copy & Freeze”. After that, when moving the cursor of the mechanical increment in the Cscan, a second image will appear. Think about changing the opacity of the scan for easier visualization (always from the “magical” right click contextual menu). Then, repeat the operation to obtain the desired number of cross-section views:
This advanced imaging capability facilitates a quick analysis of a given inspection, especially for complex flaw geometries, or when operating several series of shots with a PA probe.
Customize your layout (January 2012)
- Number and type of views displayed
- Position of the views in the analysis tab panel
- Orientation of the scan for each view
After running one simulation, a default layout (called “CEA layout”) is displayed. For instance, in the defect-response module of CIVA, the resulting analysis page shows the so-called “true Bscan” (or Sscan for phased array techniques), the 3D view and the Ascan.
However, when opening a result, you may want a specific layout for the analysis page, adding for instance a new image. CIVA offers the possibility to customize the arrangement of the different images displayed for your convenience.
For each new result displayed in a new analysis page, you will then be able to recover the specific layout.
To do that, you just need to define your new layout, and then right click on the blue “analysis” title bar at the top of the window.
Multiple possibilities are then available:
Save this new layout. Each time you wish to recover this specific arrangement, you will just have to load this layout.
Define this new layout as the default layout. This new arrangement will be the one used for all new results displayed.
Several layouts can be saved. You will be able to select your favorite layout for different simulation results.
At last, your analysis environment is really organized as you wish!
Use section views to ease flaw positioning (November 2011)
In CIVA 10, the concept of cross section views has been developed, in order to easily switch from 3D viewing into a specific 2D display. Those views are available by right clicking either on the probe or on a defect. Then, some menus allow you to select typical 2D cross section views regarding the selected object.
For instance, if you select a so-called “parallel section view” available from the flaw, you will immediately visualize the cross section view between the test piece and the flaw plane. From this new view, you are allowed to double click on the flaw to activate its interactive positioning mode, and you can easily translocate and/or rotate this flaw to put it exactly at the expected position.
You can finally go back to the 3D view with a simple click on the appropriate button, and adjust other parameters before running your simulations.
That is definitely one of the best functionalities that has been provided in the CIVA 10 release, isn’t it?
Customize your analysis environment (September 2011)
What is more bothering than a cursor which color is exactly the same as the Ascan color? Why does the second red cursor have exactly the same color as limitation markers?
Well, in the CIVA 10 release, it is now possible to customize cursor color or even image backgrounds, so that all those annoying things will not disturb you anymore!
To change the cursor’s color, nothing easier! You just need to open the “Tool > Preferences” menu, and select the “Colors” section.
Select your favorite colors for the two cursors, change the background color of Ascan and Echodynamic curves, and/or modify the color of the axis graduations…
At last your analysis environment is far more comfortable!
Enjoy your work!
Display cumulated views for phased-array inspections (July 2011)
To activate this cumulated view, just select the “data tools” option, available in the title bar of the true Bscan or Sscan image, and click on the "Cumulated view" icon:
For both of these options, the resulting image contains the complete data displayed in the image. “Merged” image means that, for each pixel of the image, the amplitude displayed corresponds to the maximum amplitude obtained in this region (if several shots correspond to this location), whereas “Mean Merged” image corresponds to the average of all shots for each pixel of the image.
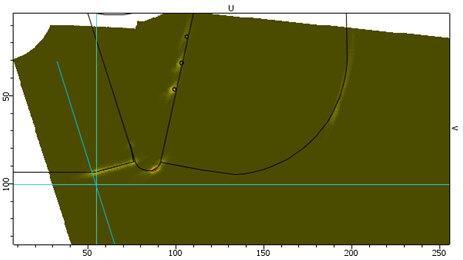
“Mean merged image”: cumulated view for all mechanical position and sectorial scanning position (average of all shots)
Define the tranduscer… Just once! (March 2011)
You can really save time using this feature as this is not so easy to access to the information relative to the probe parameters (geometry, focusing, signal,…), so… just look at the manufacturer data sheet once!
This is also an interesting feature in order to share the knowledge with your colleagues and to avoid to make some mistakes when entering input data.
How to do that ? Really simple!
Once you have filled all the information in the probe panel, just select the menu “File” then “Save” on the top left side of the panel.
Then, enter a name (well… let’s put clearly the probe reference!) and save the information, this is just a simple file that you put on your disk.
When you want to define the same probe for another project, just load all probe data from the same place with the “Open” menu, don’t spend anymore time looking for the manufacturer data sheet…
And actually this feature is available similarly for other panels: component, flaw…
Amplitude Measurement Tool (January 2011)
In the image above, it seems difficult to make an efficient measurement with a square around the tip echo (where cursors cross)!
CIVA allows the user to create a free multi point area as shown above, by clicking on the button in “data tools” available in title bars for all images.
A cross indicates the position of the maximum amplitude point in this area and a box appears and gives all available information.
Moreover, by double clicking on the area contour, the contour shape can easily be modified. This can be applied on Bscans, Cscans and so on.